3D printing with recyclable resin soon possible
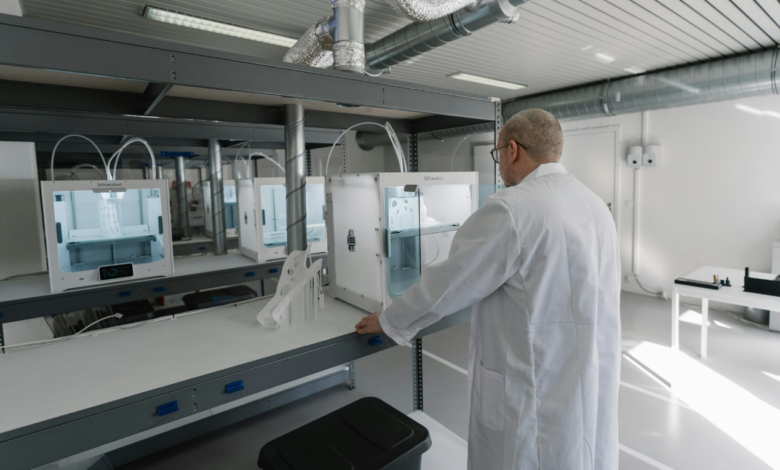
3D printing with recyclable resin is based on the lipoic acid of dietary supplements
High resolution 3D printed structures can be produced using a fully bio-based raw material. From an article published in Nature, in fact, comes the news that the University of Birmingham has tested a 3D printing with recyclable resin.
In the researchers’ experiment, once they reach the end of their useful life, products made with the printer can be recycled into an almost completely closed-loop system.
Photopolymer resins, which harden or cure with light exposure, are commonly used to manufacture custom 3D printed parts. However, while 3D printing technology has advanced considerably in terms of resolution and production speed, the resins themselves have not changed much since the 1980s. The base materials of these resins, usually epoxy or acrylic resins, derive mainly from petrochemical raw materials. Although progress has been made in the use of more sustainable resins derived from biomass, their recyclability remains limited due to the formation of irreversible bonds during hardening.
The first easily recyclable photopolymer resin
The Birmingham team managed, for the first time, to produce a high resolution printable photopolymer resin that can be broken down into its constituent parts. So, you can recycle and reprint by adding a small amount of photoinitiator. The latter serves to maintain the properties of the material.
The raw material used is lipoic acid, a naturally occurring fatty acid molecule commonly sold as a dietary supplement. The team created a combination of two lipoic acid monomers to produce a recyclable resin. In the study, the researchers completed two recycling cycles, but expected that the material could withstand others.
Potential material applications include industries that use rapid prototyping, such as the automotive industry, medical and dental components, and jewelry design.